A preventive maintenance program is key for keeping equipment in top shape. It helps avoid costly repairs and keeps operations running smoothly. By doing so, it ensures equipment lasts longer and reduces downtime.
Investing in preventive maintenance can save businesses money and improve safety. It’s about being proactive with maintenance, not just fixing things after they break. This approach can really help a company’s bottom line.
Key Takeaways
-
- Preventive maintenance programs support equipment longevity and reduce downtime
-
- The benefits of preventive maintenance include reduced operational costs and improved safety standards
-
- A well-planned preventive maintenance program helps keep equipment running smoothly
-
- Preventive maintenance enables businesses to take a proactive stance on maintenance
-
- Implementing a preventive maintenance program can have a significant impact on the bottom line
-
- Preventive maintenance programs are essential for supporting after-market services
What is Preventive Maintenance and Why It Matters
Preventive maintenance is key in managing assets. It cuts down on costs and boosts equipment efficiency. By starting a preventive maintenance plan, businesses can enjoy longer equipment life and better safety.
Big names like General Electric and Caterpillar have seen big wins with preventive maintenance. For instance, General Electric cut its maintenance costs by 25% after adopting this approach.
Key Components of Preventive Maintenance
Preventive maintenance includes regular checks, routine upkeep, and predictive methods. These parts work together to spot issues early. This reduces downtime and makes equipment more reliable.
The Role of Preventive Maintenance in Asset Management
Preventive maintenance is vital for asset management. It extends equipment life, lowers maintenance costs, and boosts efficiency. By focusing on preventive maintenance, companies keep their assets in top shape. This reduces unexpected downtime and boosts productivity.
The Financial Impact of Implementing Preventive Maintenance
Starting a preventive maintenance program can really help a company’s finances. It cuts down on downtime and lowers maintenance costs. This leads to substantial cost savings. In fact, studies show that such programs can save 10-20% on average.
Preventive maintenance offers many benefits. Some key ones are:
-
- Less downtime means more work gets done efficiently.
-
- Lower maintenance costs because problems are caught early.
-
- It also makes workplaces safer by spotting and fixing hazards.
By choosing preventive maintenance, companies can see their finances improve.
The financial benefits of preventive maintenance are clear. Companies that invest in it see a strong return. By focusing on preventive maintenance, businesses can set themselves up for long-term success and profit.
Core Benefits of Preventive Maintenance Programs
A good preventive maintenance program can greatly improve after-market services. It keeps equipment in top shape, avoiding sudden breakdowns and making it last longer. This means less downtime and more use from your assets.
Some main perks of preventive maintenance include:
-
- Extended equipment lifespan: Regular checks catch problems early, avoiding expensive fixes and replacements.
-
- Reduced operational costs: Less downtime and longer equipment life mean lower costs and better profits.
-
- Improved safety standards: These programs spot and fix safety risks, cutting down on accidents and injuries.
-
- Enhanced operational efficiency: A well-kept place runs better, wasting less and working more efficiently.
Companies that use preventive maintenance see big wins. They get safer workplaces and lower costs. For instance, it can cut down on energy use and bills, saving money. By choosing preventive maintenance, companies keep their gear running well, supporting their service goals.
In short, a preventive maintenance program is key for after-market services. It supports equipment from start to finish, ensuring it works its best.
Corrective Maintenance vs Preventive Maintenance: Understanding the Difference
There are two main ways to keep equipment and assets in good shape: corrective maintenance and preventive maintenance. These methods are key for businesses looking to improve their maintenance plans. Corrective maintenance fixes or replaces equipment after it breaks down. On the other hand, preventive maintenance focuses on regular upkeep to stop equipment from failing.
Preventive maintenance has big benefits. It cuts down on downtime and lowers costs compared to corrective maintenance vs preventive maintenance. Regular maintenance helps spot and fix problems early. This makes equipment more reliable and less likely to fail unexpectedly.
Preventive maintenance shines in certain situations:
-
- High-value equipment or assets that are crucial to business operations
-
- Equipment with complex systems or components that are hard to repair
-
- Industries with strict safety rules or standards, where equipment failure can be serious
But, corrective maintenance vs preventive maintenance might be better for non-essential equipment or where maintenance costs are low. Still, preventive maintenance is usually the smarter choice for keeping equipment and assets in top shape.
Knowing the difference between corrective maintenance and preventive maintenance helps businesses choose the best maintenance strategy. This leads to less downtime, lower costs, and better efficiency overall.
Maintenance Approach | Benefits | Drawbacks |
---|---|---|
Corrective Maintenance | Lower upfront costs | Higher costs in the long run, increased downtime |
Preventive Maintenance | Reduced downtime, lower costs, improved equipment reliability | Higher upfront costs, requires regular maintenance scheduling |
Building an Effective Preventive Maintenance Schedule
Creating a preventive maintenance schedule is key to getting the most out of preventive maintenance. A good plan ensures maintenance is done right and on time. This cuts down on downtime and boosts productivity.
Determining Maintenance Frequency
To figure out how often to do maintenance, look at how often the equipment is used. Also, check what the manufacturer says and what others in the industry do. This helps make a schedule that fits both maintenance needs and production goals.
Resource Allocation Strategies
It’s important to manage resources well to keep maintenance on track. This means having the right people, materials, and tools ready. Preventive maintenance can also lower costs and make things safer.
Here are some ways to manage resources:
-
- Focus on the most important maintenance tasks first
-
- Assign resources based on how often and long maintenance takes
-
- Use software and tools to keep track of maintenance
Documentation and Record Keeping
Maintenance Activity | Frequency | Personnel |
---|---|---|
Equipment Inspection | Weekly | Maintenance Team |
Parts Replacement | Monthly | Maintenance Team |
By following these steps and thinking about preventive maintenance’s benefits, companies can make a schedule that works for them. This schedule meets their specific needs and goals.
Technology and Tools in Modern Preventive Maintenance
Modern preventive maintenance uses a lot of technology and tools. These help make maintenance programs better and more efficient. A good preventive maintenance program can plan maintenance well, predict problems, and make equipment work better.
Some new technologies in preventive maintenance are predictive maintenance software and IoT devices. These tools let us watch equipment and systems in real time. They help us find problems early and fix them before they get worse. This way, equipment lasts longer and works better.
Using technology and tools in preventive maintenance brings many benefits:
-
- Equipment works better and is more reliable
-
- Maintenance costs go down and downtime is less
-
- Safety standards and rules are followed better
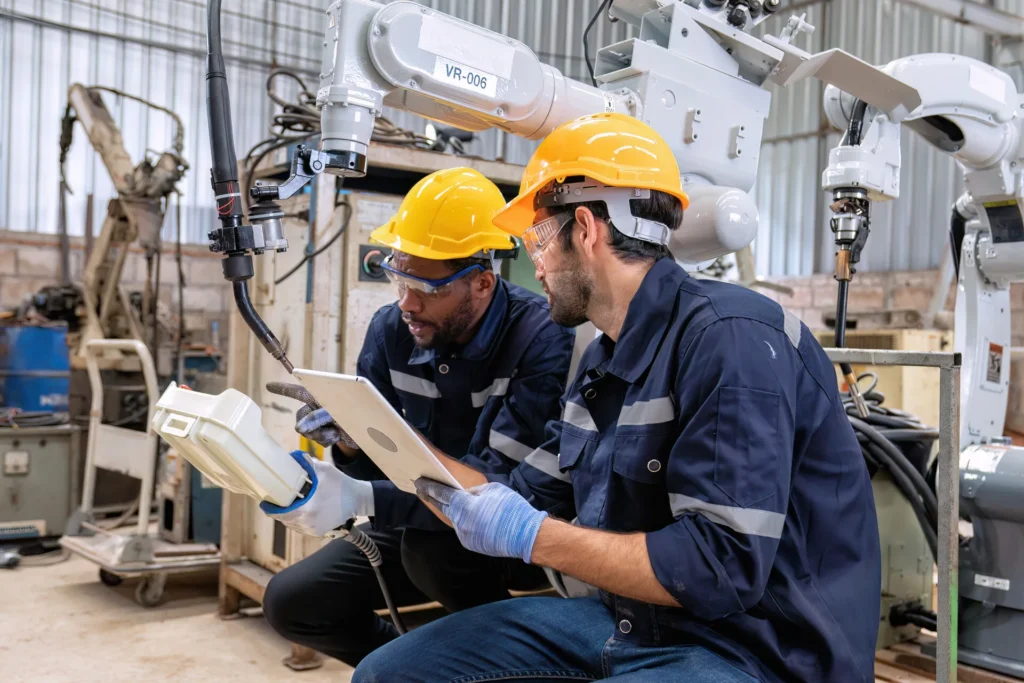
By using these technologies and tools, companies can create a strong preventive maintenance program. This program can make things more efficient, save money, and improve performance overall.
Measuring the Success of Your Preventive Maintenance Program
To see if a preventive maintenance program works, it’s key to watch certain key performance indicators (KPIs). These KPIs show how well preventive maintenance does its job. They include things like less downtime, saving money, and better equipment reliability.
Some common metrics used to measure the success of preventive maintenance programs include:
-
- Mean Time Between Failures (MTBF)
-
- Mean Time To Repair (MTTR)
-
- Overall Equipment Effectiveness (OEE)
These metrics give us important insights into how well the maintenance program is doing. They help us find areas that need better focus.
By checking and analyzing these metrics often, companies can make their maintenance plans better. They can use resources more wisely and get the most out of preventive maintenance. This way, businesses can make smart choices, cut down on maintenance costs, and work more efficiently.
With a strong preventive maintenance program and tracking key performance indicators, companies can reach their full potential. They can reduce downtime and save a lot of money. This leads to better profits, more competition, and lasting success.
Common Challenges and How to Overcome Them
Organizations often face challenges when starting preventive maintenance programs. One big issue is resistance to change. Some employees might doubt the benefits of preventive maintenance. It’s key to teach them why it’s important and how it boosts efficiency and cuts downtime.
Another hurdle is limited resources, like budget and staff. To tackle this, focus on the most critical equipment and systems. You might also think about hiring outside help or using tech to make maintenance smoother.
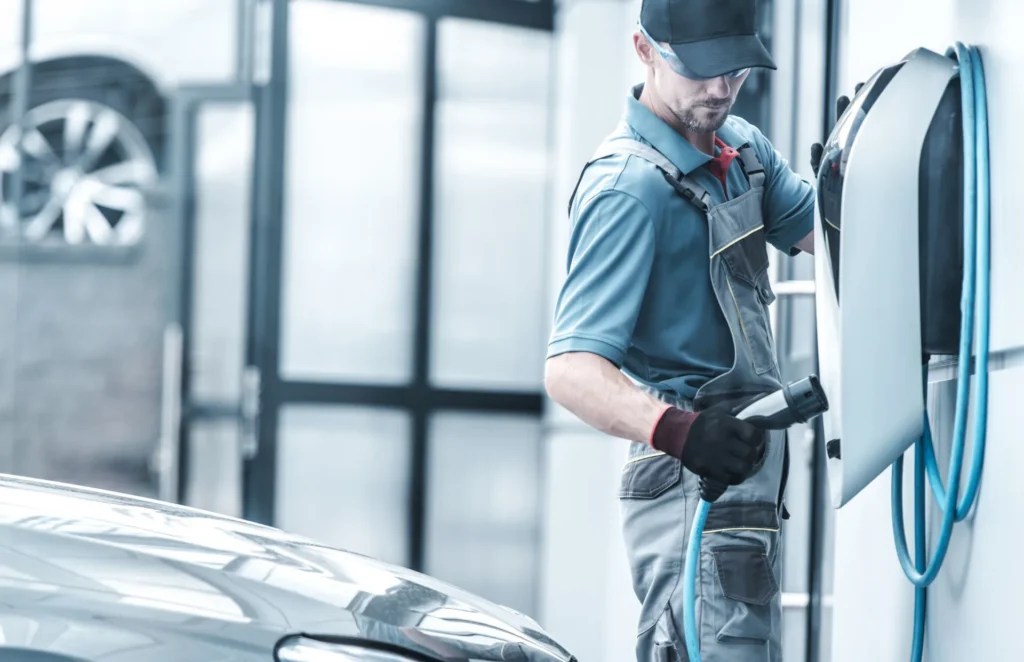
-
- Difficulty in measuring effectiveness: Use key performance indicators (KPIs) to track the success of the preventive maintenance program.
-
- Lack of resources: Prioritize maintenance tasks and consider outsourcing or using technology to optimize resources.
-
- Resistance to change: Educate employees on the benefits of preventive maintenance and involve them in the implementation process.
By tackling these common challenges, organizations can succeed with preventive maintenance. This leads to better efficiency, lower costs, and safer work environments.
Conclusion: Taking the Next Step in Your Maintenance Strategy
A strong preventive maintenance program brings many benefits to businesses. It helps keep equipment running longer, cuts down on costs, and boosts efficiency. The advantages of preventive maintenance are clear, making it key for any maintenance plan.
It’s time to move forward. Whether starting a new program or improving an old one, begin with small steps. Track your progress and keep making your processes better. This proactive approach will protect your equipment and help your business grow.
Preventive maintenance is more than a good idea; it’s essential. It opens doors to growth, better customer service, and staying competitive. Start this journey now and see how your maintenance operations become a major advantage.