What does maintaining legacy products mean in electronics?
In electronics, the term “legacy” typically refers to systems or hardware that are no longer in mainstream use or are outdated. Legacy systems or hardware may include products that were once popular or widely used but have since been replaced by newer, more advanced technologies. These outdated products may still be functional and may even have a dedicated user base, but they are no longer actively sold or supported by manufacturers. Legacy hardware typically includes components or devices that are no longer produced, making it challenging to find replacement parts or receive official repair services.
However, third-party vendors or specialized technicians often can offer repair services for legacy hardware. Despite being outdated, legacy systems and hardware can still serve a purpose for those who rely on them or prefer their functionality. Many businesses and industries may still utilize legacy systems due to factors such as cost, compatibility, or specialized functions. In these cases, the challenge becomes maintaining and extending support for these systems, especially as technology and software advance.
Some companies may upgrade to newer systems or hardware to avoid issues with compatibility or diminishing technical support. However, others may choose to continue using legacy systems but invest in third-party maintenance services to ensure continued operation. Ultimately, legacy systems and hardware can be seen as a reminder of the progress made in the field of electronics and the ever-evolving nature of technology. While they may no longer be at the forefront of innovation, legacy products, and systems continue to serve distinct purposes for individuals and organizations that rely on them
What is one problem with maintaining legacy systems?
Maintaining legacy systems poses a significant challenge for organizations in today’s rapidly evolving technological landscape. One problem associated with these outdated systems is the lack of vendor and component availability. As technology advances and newer systems are introduced, vendors often discontinue support for older versions or completely phase out the product.
This leaves organizations relying on legacy systems without the necessary updates, patches, and bug fixes crucial for ensuring system stability and security. Without vendor support, organizations face an increased risk of vulnerabilities and potential cyber threats, as the vendor will not address any new security vulnerabilities that may arise. Additionally, without access to a reliable support system, organizations may find it difficult to troubleshoot and resolve any issues with the legacy system. They may be required to rely on their in-house team, which may have limited knowledge and expertise in dealing with outdated technologies.
Another problem with maintaining legacy systems is difficulty integrating with newer technologies. Organizations striving to stay ahead in the competitive market must adopt new technologies and applications to streamline their processes and increase efficiency. However, legacy systems are not designed to seamlessly integrate with these modern tools, making it challenging to leverage their benefits. This can result in inefficiencies, duplication of efforts, and fragmented systems, hindering the organization’s ability to adapt and evolve with changing business requirements.
Moreover, legacy systems can also lead to increased operational costs for organizations. Since these systems are outdated, they require specialized skills and resources to maintain their functioning. Hiring and retaining personnel with expertise in legacy systems can be costly, as their skill sets may not align with the latest technological advancements. Additionally, sourcing replacement parts or repairing hardware can be expensive and time-consuming, as these components may no longer be available in the market. The effort required to keep legacy systems operational and productive can divert resources and investments from more strategic initiatives, potentially limiting the organization’s ability to innovate and grow in a competitive landscape.
How do you handle legacy systems?
When handling legacy systems, it is essential to approach the task with a systematic and strategic mindset. Legacy systems are typically older systems, applications, or software that have been used for a significant period and still serve a critical function within an organization.
The first step in handling legacy systems is to thoroughly assess the system’s capabilities, limitations, and dependencies. Understanding the system’s architecture, technology stack, and integration points is crucial for developing an appropriate strategy. Once the assessment is complete, it is essential to prioritize the risks and challenges associated with the legacy system. This involves identifying areas of potential failure, security vulnerabilities, and performance bottlenecks. Based on these prioritized risks, a roadmap can be developed for gradually modernizing or replacing the legacy system.
This roadmap should include short-term and long-term goals and a detailed plan of the necessary actions, resources, and timelines. It is also crucial to involve the stakeholders and users of the legacy system in the decision-making process and keep them informed about the proposed changes.
Monitoring and continuous evaluation of the legacy system are essential to identify any new risks or challenges that may arise. Regular maintenance, updates, and security checks should also be performed to ensure the legacy system’s stability and mitigate potential security breaches. By following a well-thought-out strategy, organizations can effectively handle legacy systems while minimizing disruptions and maximizing the system’s lifespan and efficiency.
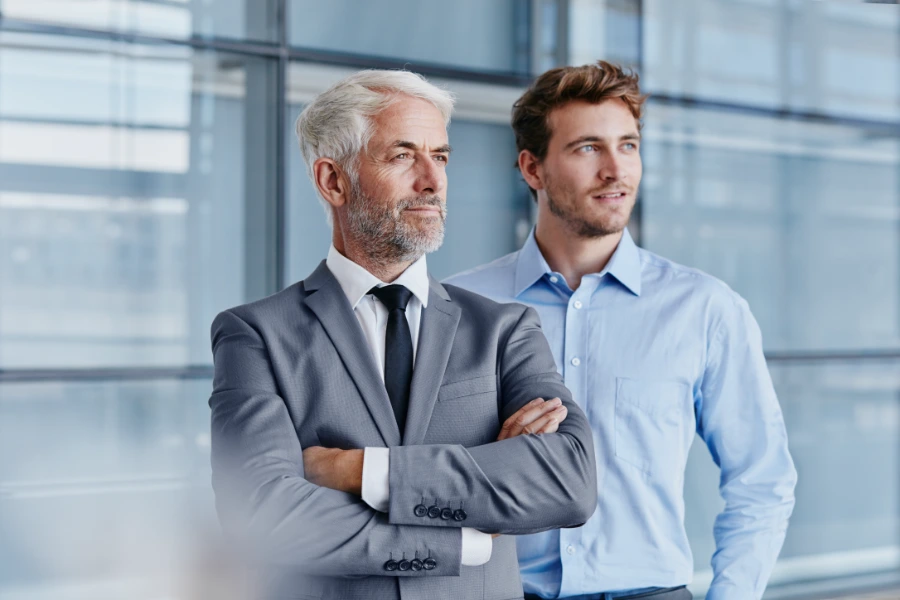
Today there are Two Main Options: REPAIR OR LICENSE.
In today’s economy, OEMs are faced with continuously reducing product lifespans. Customers expect new products every several years. Long gone are when a product has a lifespan of over 15 years. Simultaneously, the pressure is rising on reducing Engineering headcount and redesigning products because of reduced component lifespan. Some industrial customers expect available repair services for products for over ten years after the last product was sold. These issues force OEMs to make large investments or find a reliable partner to help.
Let us have a quick look at the available options.
HARDWARE REPAIR SOLUTIONS:
Customers expect a good experience and to be cared for in the best possible way. They may even require getting a replacement part installed at their premises.
Some massive investments or finding a partner for the process are needed. The right partner can help improve your customer aftermarket experience: Customers have high expectations regarding receiving a satisfactory experience and being effectively attended to. They may even need a replacement component to be installed at their location.
Significant investments or finding a suitable partner is necessary to manage this process. By partnering with the right company, you can increase the quality of your customer’s post-purchase experience.
Flexible and straightforward product routing with ease-of-use data capture for failure analysis—warranty validation, RMA creation and generation, and contact center functionality. At the same time, you need to ensure that your products are repaired correctly, minimize repeat returns, and reduce your warranty costs.
Full track and trace with carrier integration and remote stock holding and reporting. If done right, this can maximize the value of your returns. Streamlined returns and triage not only speed up turnaround and response time, they also reduce scrap and recapture the value of your assets. The parts must be remanufactured or reconditioned to be “like new.”
You need to scale globally and strategically to provide rapid turnaround in every region, minimizing your investment in swap inventory and mitigating your transportation costs. The right partner will receive, inspect, refurbish, repair, and redistribute products, providing a single, simplified point of contact for all your reverse logistics needs.
LICENSING FOR PRODUCT CONTINUITY:
In this model, the partner fully owns the legacy products.
Product Licensing is a bold move that enables OEMs to focus on its core
• new product evolution and development
• while providing a robust customer service model for older products.
OEMs need to devote their R&D resources and personnel to developing new technologies. This process involves assessing whether a product or product line is still core to its overall strategy. That said, it’s imperative to continue serving customers who rely on older products with decades-long lifecycles. This presents a Catch-22: an OEM typically does not have the resources (i.e., cash, working capital, armies of engineers) to develop new products and continue meeting customers’ high expectations for the service and support of older products.
Licensing also minimizes product support costs for legacy products, provides ongoing, experienced customer support for mature product lines, and funds future R&D.
Whatever solution is best for you, keeping the end customer in mind and offering them a flawless process to ensure they return is essential.
Conclusion:
You have some tough decisions when dealing with “legacy systems” or older technology. You’ve got technology improving at warp speed, customers always wanting the latest gear, and you need to manage your resources wisely.
We can tackle these issues in two key ways: hardware repair solutions or product licensing.
The hardware repair route means you’ve got to invest quite a bit or team up with a partner who knows their business. Your goal is to keep your customers happy – they might even want a replacement part delivered and installed at their site. The right partner can help by ensuring repairs are done right the first time, reducing the number of repeat fixes, and bringing down warranty costs.
This approach’s key aspect is ensuring that old parts are as good as new. You’ve got to be agile, ready to offer quick turnarounds everywhere. This means you’ll spend less on extra inventory and save on shipping costs. To pull this off, you need a partner who handles returns, refurbishing, repairing, and redistributing products.
The alternative approach is product licensing. This one’s a bold strategy that lets original equipment manufacturers (OEMs) keep their eyes on the prize – developing new products. Here, the partner handles the old products, freeing up OEMs to focus on developing the next big thing.
This is a double win: you’re spending less on supporting older products while still offering great customer service for the older product lines. Plus, you’re freeing up funds for future research and development.
Whichever path you choose, remember the end customer is king. They’re more likely to stick around if you can give them a smooth experience. So, the best solution should solve the company’s issues and keep the customer’s needs at the forefront, ensuring those legacy systems keep ticking along just fine.
Frequently Asked Questions
What is the importance of maintaining legacy systems?
Maintaining legacy systems is crucial to ensure business continuity and product continuity. Legacy systems often support manufacturing and other critical processes in organizations.
What are the challenges companies face when maintaining legacy systems?
Companies may encounter the following challenges when maintaining legacy systems:
• High product support costs
• Managing mature product lines
• Dealing with a rapidly changing technological landscape
• Addressing changing market conditions
How can companies reduce the cost of maintaining legacy systems?
Companies can reduce the cost of maintaining legacy systems by implementing digital transformation initiatives, streamlining processes, and leveraging newer technologies that can replace or integrate with legacy systems.
What are the benefits of maintaining legacy systems?
Maintaining legacy systems allows organizations to extend the lifespan of their investments, utilize existing infrastructure, address customer expectations, and capture validation in regulated industries.
What does it mean to maintain legacy products?
Maintaining legacy products involves providing ongoing support, repair, and replacement services for outdated hardware, software licenses, and other components of enterprise systems.
Why is it important to rely on the expertise of a trusted supplier for legacy system maintenance?
Legacy system maintenance requires specialized expertise and knowledge. Relying on a trusted supplier ensures that the necessary skills are available to deal with the complexities of legacy systems.
What role does legacy system maintenance play in ensuring compliance?
Maintaining legacy systems is critical for organizations operating in regulated industries as it helps ensure compliance with industry-specific requirements and standards.
How can legacy system maintenance enhance an organization’s overall security?
Legacy system maintenance involves securing critical components and infrastructure from vulnerabilities and threats. Organizations maintain a secure core environment by regularly patching and updating these systems.
How does legacy system maintenance impact logistics and supply chain management?
Effective legacy system maintenance enables organizations to manage inventory and equipment logistics efficiently. This improves the supply chain and ensures timely delivery of the necessary components.