System Assembly
Box build assembly is a critical component of modern manufacturing processes. This comprehensive process combines components into a final product, including designing and manufacturing mechanical boxes, PCB assembly, wiring cables, testing end products, and labeling. Box build assembly services can be tailored to meet specific requirements and offer several benefits, such as cost reduction, improved work quality and productivity, quality assurance, and simplified supply chain management.
The importance of box-build assembly lies in its ability to streamline the production process by handling all aspects of the final product’s integration. This means manufacturers can focus on their core competencies while outsourcing other necessary tasks to specialized companies. As a result, they can achieve greater efficiency in terms of time and resources while maintaining high-quality standards. Manufacturers must understand the full scope of box build assembly to ensure a successful implementation meeting their unique needs.
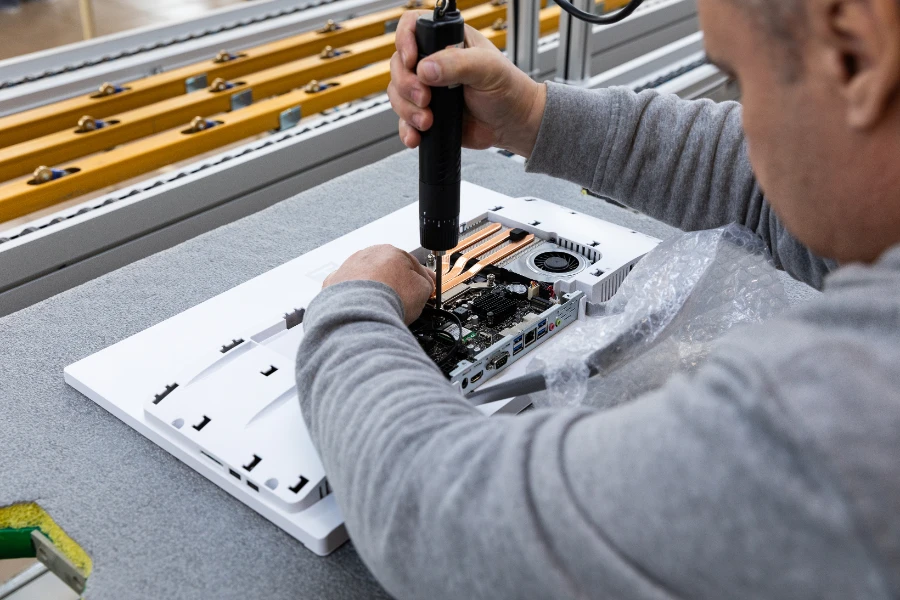
The Importance of System Assembly in Manufacturing
Box build assembly plays a critical role in manufacturing as it involves integrating PCBAs into enclosures, wiring cables, testing end products, and labeling to ensure safe and efficient product performance. This full-service box build process includes managing related SOP operation standards, station self-inspection, QC full inspection, QA spot sampling, and pre-shipment OBA sampling inspection. The box-build assembly process involves creating a device, integrating system post-assembly processes, specifications and requirements, and testing.
One of the advantages of box-build assembly is that it offers a one-stop solution for customers looking to simplify their supply chain. Box build manufacturers provide services ranging from PCB manufacturing to parts procurement, PCB SMT assembly, testing and shipping. By outsourcing these services to an experienced provider with strict quality control measures in place – companies can reduce production costs while improving work quality and productivity.
Materials selection is an important aspect of box build assembly as different materials have varying properties such as durability or heat resistance. Depending on the application requirements, boxes can be made using materials such as ABS plastics or sheet metal. This stage also considers customer requirements to ensure the final product meets all necessary criteria.
Quality control is crucial throughout the entire box build assembly process to ensure each unit performs reliably over time. Thorough requirements gathering at the beginning of the project helps model the assembly process as a whole so that potential issues can be addressed early on. Testing protocols, including functional testing, IC programming, and conformal coating thermal aging testing, are performed before shipping out units to guarantee optimal performance upon delivery.
Box build assembly provides a comprehensive approach to assembling electronic products by creating a device from scratch through integration into enclosures followed by rigorous quality control measures. By providing advantages like cost reduction while simultaneously upgrading work productivity due to high-level tests conducted at every step, materials selection depends on customer needs which are thoroughly considered during the initial stages and thorough requirement gathering for each project.
Understanding the Components Involved in Box Build Assembly
Integrating various components in electronic products involves a range of specialized tasks, such as designing and manufacturing mechanical enclosures, wiring cables, testing end products for functionality, and applying quality assurance measures. Design considerations are crucial in ensuring the enclosure is compatible with the product’s dimensions and meet the necessary safety requirements. Material selection is also an important factor to consider since it affects the durability and overall quality of the final product. Common materials used for enclosures include ABS plastics and sheet metal.
During the assembly process, sub-assemblies are created by interfacing different components using ribbon cables, electrical wire, and connectors, among other methods. Final enclosure assembly involves fastening parts using riveting screws, nuts and bolts or welding, depending on the material choice. The resulting device is subjected to thorough testing protocols to ensure all systems operate correctly before being released into the market. Quality control measures such as station self-inspection, QC full inspection, and QA spot sampling inspection are implemented during box build assembly to minimize errors.
Overall, box build assembly requires expertise across various fields, such as mechanical engineering teams in OEM companies that oversee design considerations and material selection processes. At the same time, EMS or CEM usually handle PCB assemblies. In addition to these benefits provided by outsourcing manufacturers- reduction in production costs improved work quality & productivity, all while taking care of supply chain simplification – proper communication between assembler/manufacturer OEM/ODM regarding requests helps create a satisfactory result for clients seeking simple or complex box builds alike with their specific needs fully considered throughout every stage from PCB fabrication through warehousing post-delivery service support.
Tools and Equipment Required for Box Build Assembly
Efficient and effective box-build assembly requires the utilization of a variety of specialized tools and equipment. These tools are necessary to ensure the product meets industry standards, is assembled correctly, and functions properly. Some essential equipment requirements for box build assembly include:
- Soldering stations: used to connect components on a PCB.
- Power supplies: provide voltage and current to circuitry during testing.
- Multimeters measure electrical properties such as resistance, voltage, and current.
- Oscilloscopes: display waveform signals generated by electronic devices.
Safety precautions should also be taken when working with these tools and equipment. Operators should wear appropriate personal protective equipment (PPE) such as gloves, safety goggles, or masks to protect themselves from hazards like chemicals or soldering fumes. Additionally, training programs must be provided to teach workers how to operate the equipment safely.
Workflow optimization is another important consideration in box build assembly. The production line layout should be optimized for efficient movement of materials between stations while minimizing errors. This can be achieved by implementing lean manufacturing principles or using software tools like Computer-Aided Manufacturing (CAM).
Maintenance strategies must also be established to ensure the tools and equipment remain in good condition over time. Regular cleaning and calibration checks are important steps in preventing malfunctions or breakdowns during production.
In summary, achieving quality results in box build assembly requires careful attention to equipment requirements, safety precautions, workflow optimization, and maintenance strategies. By investing in these areas, manufacturers can improve their efficiency while delivering products that meet customer expectations for reliability and performance.
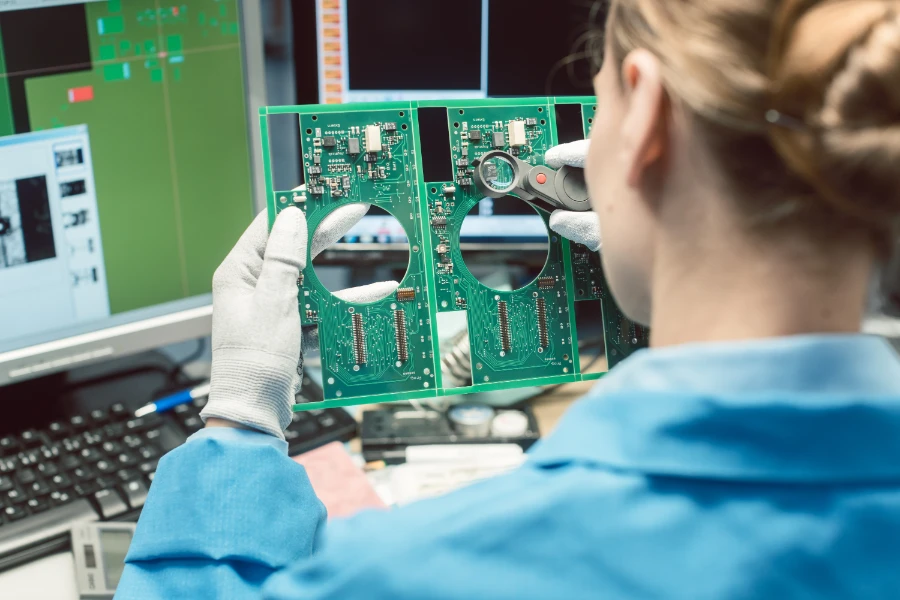
Best Practices for Ensuring Quality Control in Box Build Assembly
Achieving optimal results in the manufacturing process of electronic products requires strict adherence to quality control measures throughout every stage of production, from design to delivery. Box build assembly is no exception and ensuring that the final product meets all requirements and specifications is vital. Quality control measures are crucial for defect prevention, and they involve a range of techniques, such as inspection, testing protocols, and assembly standards.
One critical aspect of quality control in box build assembly is inspecting all components before integration into the final product. This inspection should cover everything from PCBs to cables, connectors, enclosures, and any other parts required for the assembly process. Verifying that every component meets specified standards is essential before proceeding with integration. This step helps identify potential issues early on and prevent them from escalating.
Quality control in box build assembly ensures proper testing protocols are followed during each production stage. Testing should be done at different assembly levels to verify functionality and performance. This includes sub-assembly testing, system-level testing, pre-shipment OBA sampling inspection, and other tests required by client requests or internal QC processes.
Adherence to industry-standard assembly practices ensures optimal quality in box-build assemblies. It’s crucial to strictly follow SOP operation standards throughout the process while implementing management methods such as station self-inspection or full QC inspections where necessary. Doing this consistently at every stage of production ensures that defects are caught early, saving time and costs associated with fixing errors later on.
In conclusion, achieving high-quality results in box build assemblies requires strict adherence to a range of quality control measures throughout every stage of production: inspection techniques for verifying each component meets set standards; implementation/testing protocols at various levels (sub-assemblies/system level) demonstrating functionality/performance; following industry-standard best practices during the entire process which can reduce costs/time spent correcting issues later down the line. By following these measures consistently, manufacturers can ensure that their box-build assemblies meet all requirements and specifications, resulting in a high-quality product that meets the end user’s needs.
Common Challenges Faced in Box Build Assembly and How to Overcome Them
One of the significant challenges encountered during the manufacturing process of electronic products’ final stage is dealing with complex integration issues that require specialized expertise to overcome. Assembling a complete box build involves integrating various components, including PCBs, cables, and enclosures, which can be challenging due to different assembly requirements. Moreover, selecting appropriate materials for each component ensures optimal functionality and performance.
To overcome these challenges, manufacturers must optimize their assembly processes by selecting suitable materials and testing techniques. For instance, incorporating advanced testing methods such as X-ray inspection can help identify any hidden defects in the assembled product. Additionally, implementing strict quality control measures throughout the manufacturing process is crucial for identifying potential issues early on and preventing them from escalating into more severe problems.
Another challenge that manufacturers face during box build assembly is ensuring proper communication between the mechanical engineering team and electronic engineers involved in designing and assembling the product. This requires effective stakeholder collaboration to ensure seamless integration of all components. Regular meetings or project management tools can establish effective communication channels to track progress.
While box build assembly presents several challenges for manufacturers in integrating various components, optimizing their processes through material selection and testing techniques can help mitigate these issues effectively. Implementing strict quality control measures at every production stage ensures that potential defects are identified early on before they result in costly recalls or repairs. Effective communication channels among team members involved in designing and assembling the product also play a critical role in ensuring successful box-build assembly projects.
Cost-Effective Strategies for Box Build Assembly
In the previous subtopic, we discussed some common challenges faced during box build assembly and how to overcome them. Now, let’s explore cost-effective strategies that can be employed in this process. As with any manufacturing process, reducing costs is essential for maximizing profits. However, it should not come at the expense of quality assurance measures.
One way to reduce costs is by streamlining processes. This involves identifying areas where unnecessary steps or bottlenecks cause delays and inefficiencies. Manufacturers can save time and resources by optimizing these processes while improving overall productivity. For example, automating certain tasks, such as cable cutting or testing, can significantly reduce labor costs.
Another strategy for cost reduction is material optimization. This involves finding ways to use materials more efficiently without compromising quality or performance. Manufacturers can achieve this by choosing more durable and longer-lasting materials or using recycled materials where possible.
Supplier management is also crucial in reducing costs in box build assembly. By building strong relationships with suppliers and negotiating favorable terms, manufacturers can save money on raw materials and components while ensuring consistent quality standards.
Quality assurance measures should not be overlooked when trying to reduce costs in box build assembly. Cutting corners on testing or inspection procedures may result in defective products that require costly rework or repairs. To avoid this scenario, manufacturers must develop robust quality control systems that regularly audits suppliers’ facilities and product inspections throughout production.
Implementing cost-effective strategies such as streamlining processes, material optimization, supplier management, and quality assurance measures can help manufacturers balance reducing costs and maintaining high-quality standards in box-build assembly.
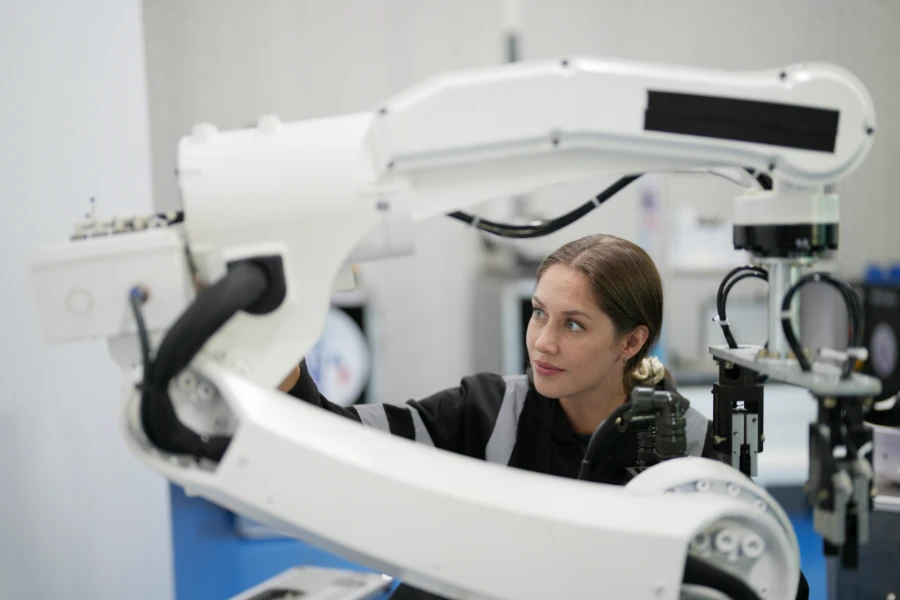
The Role of Automation in Box Build Assembly
Automation plays a significant role in increasing efficiency and reducing costs in the manufacturing process of electronic products. Automated machines and software can reduce production time, eliminate errors caused by human factors, and improve product quality. Automated systems are particularly useful in box-build assembly, where complex assemblies must be manufactured with high accuracy and reliability.
Implementation challenges are one of the significant barriers to adopting automation in box build assembly. Integration techniques such as modular design, standardization of components, and open architecture can help overcome these challenges by allowing different systems to communicate seamlessly. Another challenge is the need for skilled technicians to operate automated systems effectively. Training programs for employees can help bridge this knowledge gap.
Quality control methods ensure that automated processes consistently produce high-quality products. Testing equipment such as functional testers, ICT (in-circuit test), AOI (automatic optical inspection), and X-ray inspection tools can detect defects early in manufacturing, saving time and materials. Real-time monitoring of production processes using sensors can also identify potential issues before they become costly problems.
Future advancements in automation technology will continue to impact box build assembly positively. Advances in robotics, machine learning algorithms, and augmented reality tools for training technicians on new machinery will quickly revolutionize the industry’s productivity through increased efficiency levels while lowering labor costs associated with both manual workforces or outsourcing services abroad, where wages may be cheaper than what would have been paid domestically otherwise due to lower labor standards outside developed countries like America or Europe.
Environmental Considerations in Box Build Assembly
Environmental sustainability is a pressing concern in the manufacturing industry, and implementing eco-friendly practices in the production process of electronic products can have a significant positive impact on the planet. This has led to an increased focus on environmental considerations in box-build assembly. Some of the key ways that manufacturers are striving to reduce their environmental footprint include:
- Sustainable materials: Manufacturers are exploring alternative materials more sustainable than traditional options, such as plastics made from renewable resources and biodegradable materials.
- Energy efficiency: Box build assembly facilities incorporate energy-efficient lighting, HVAC systems, and equipment into their operations to minimize their energy consumption and reduce their carbon footprint.
- Waste reduction: Techniques such as lean manufacturing and just-in-time inventory management minimize waste and ensure that only necessary materials are used during production.
- Recycling methods: Many manufacturers have implemented recycling programs for internal wastes generated during production processes and end-of-life products. This includes implementing closed-loop recycling systems for certain materials.
In addition to these voluntary initiatives, various environmental regulations govern box-build assembly processes. For example, many countries have strict hazardous materials and waste disposal regulations. Compliance with these regulations is not only important for protecting the environment but also for avoiding legal consequences. Overall, there is growing recognition within the industry of the importance of reducing its environmental impact through sustainable practices in box-build assembly.
Future Trends in Box Build Assembly Technology
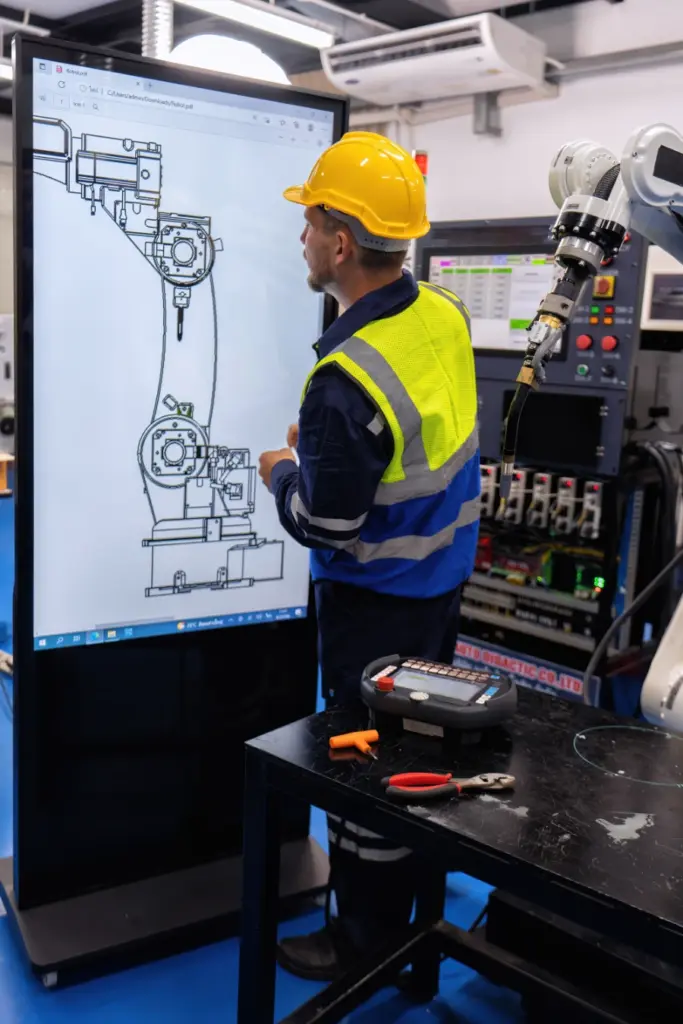
Advancements in technology are expected to greatly impact the manufacturing process of electronic products, particularly in areas such as design and testing. Integrating artificial intelligence (AI) into box-build assembly processes is a major trend. AI can aid manufacturers in identifying defects, predicting failures, and optimizing production schedules for maximum efficiency.
Another trend is adopting smart manufacturing systems, which use data analytics and machine learning techniques to continuously improve the production process. These systems allow for real-time monitoring of equipment performance, identifying potential issues before they occur, and optimizing workflows based on changing demand.
Advanced robotics are also being increasingly utilized in box-build assembly processes. Robotics can perform tasks that require high precision and speed while reducing human error. They also enable greater flexibility in production lines by allowing for easy reconfiguration to accommodate product specifications or demand changes.
Lastly, IoT-enabled devices are integrated into box-build assemblies to provide real-time performance and usage patterns feedback. This data can be used to improve product design and optimize maintenance schedules and identify potential issues before they become critical.
Overall, industry 4.0 implementation drives significant changes in box-build assembly technology by integrating AI, smart manufacturing systems, advanced robotics, and IoT-enabled devices. These trends promise increased efficiency, productivity improvements, and higher quality products with fewer defects while reducing costs associated with manual labor-intensive workloads, all leading towards a more sustainable future for the electronics manufacturing industry as a whole.
Case Studies: Successful Implementations of Box Build Assembly
The future of box-build assembly technology looks promising, with advancements in automation and integration benefits. However, it is important to note that successful implementations of box-build assembly have already been achieved in various industries. These case studies demonstrate the effectiveness of box build assembly as a cost-effective solution for manufacturing complex electronic products.
One industry that has benefited greatly from box build assembly is the medical industry. The strict quality control measures required for medical devices make box-build assembly ideal for ensuring product safety and reliability. Additionally, the customizable nature of box builds allows for specific features to be integrated into medical devices, such as sensors and software programs.
Another industry where box-build assembly has proven successful is telecommunications. With the increasing demand for efficient communication systems, telecom companies require fast and reliable production processes. Box build assembly offers just that: its streamlined process and ability to integrate complex electronic systems quickly.
Furthermore, automotive manufacturers have also successfully implemented box build assemblies into their production lines. As cars become more technologically advanced, the need for intricate electronic systems increases exponentially. Box builds allow these systems to be assembled quickly and efficiently while maintaining high levels of quality control.
These case studies demonstrate how box build assembly can benefit various industries through its cost-effective solutions and reliable quality control measures. As technology advances, we can only expect further developments in this field that will continue to improve manufacturing processes across multiple sectors.
Table of Contents
Frequently Asked Questions
Lead time estimation for completing an assembly project depends on various factors such as project management, quality control, component sourcing, and assembly optimization. The average time frame can range from weeks to months, depending on the project’s complexity.
Electrostatic protection measures must be implemented during the assembly line setup to prevent damage to electronic components. Workers should receive proper training techniques, and testing protocols must be established. Strict quality control standards are necessary for ensuring product safety and reliability.
The most common materials used for PCB enclosures include ABS plastics and sheet metal due to their durability, cost-effectiveness, and customizability. Material selection also considers aesthetics to ensure the final product meets customer expectations.
Abnormalities or incorrect polarity during battery welding in the assembly process can be handled through quality control measures such as regular checks and testing. Trained technicians can do polarity correction, while process improvement can prevent future occurrences.
The typical warranty period offered for electronic products varies depending on the manufacturer. Warranty coverage usually includes repair or replacement options, with customer support and return policies in place to ensure a smooth process.